[Over to… Giovanni Belia, Sales Director of Lucy Plast SpA
Plastic: an infinite resource
by
Lucy Plast
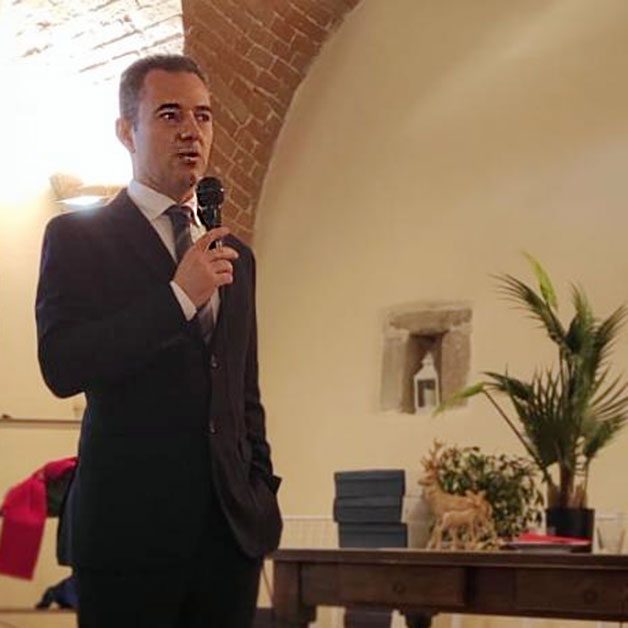
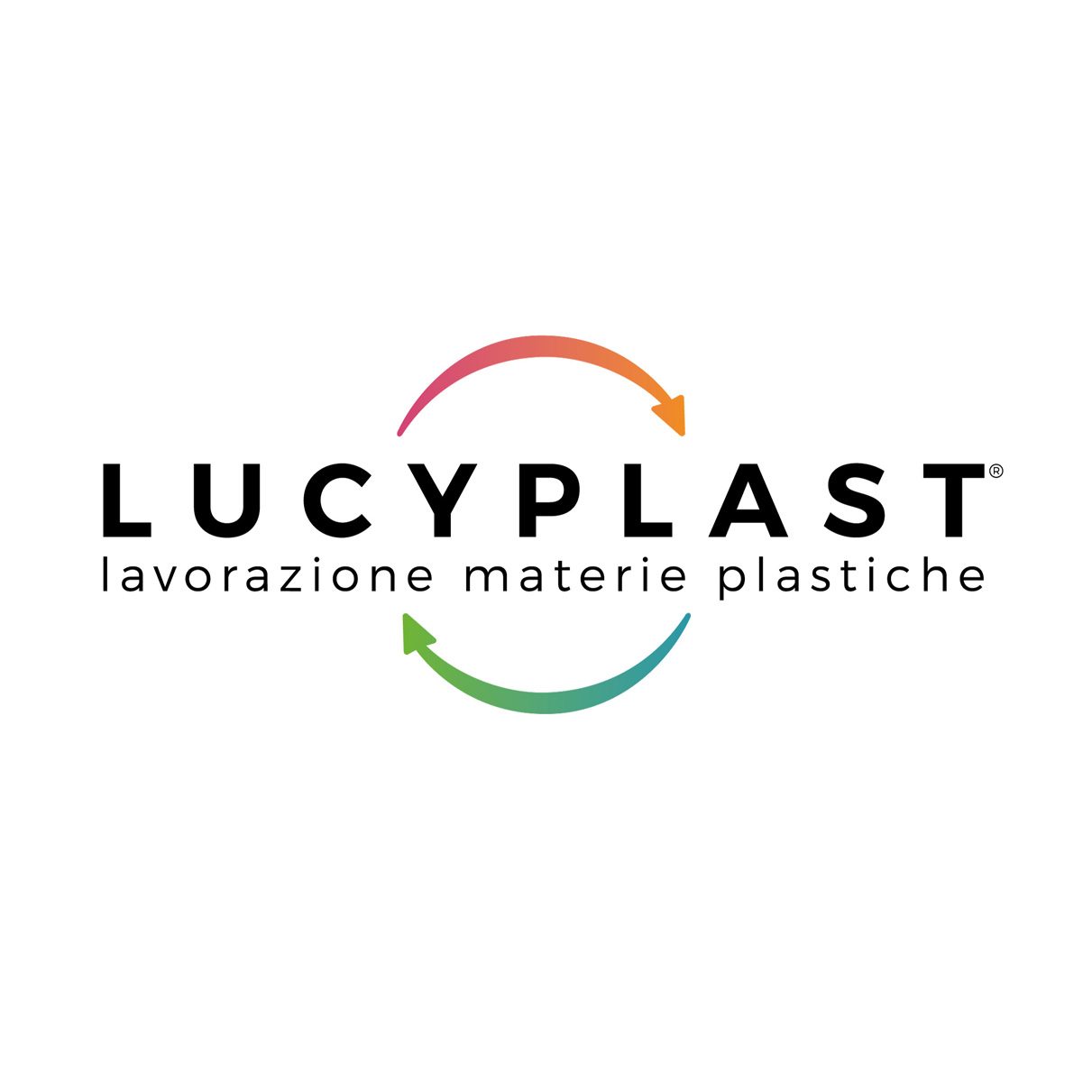
«Over 4,000 tonnes of waste transformed into long-lasting and ecological packaging: this figure, updated in 2022, gives a precise idea of Lucy Plast’s field of specialization.
We deal with collection, recycling, regeneration in granules and injection moulding. We use secondary raw materials traced at the origin, coming from industrial and post-consumer sources.
The company was established in 1977 for regenerating plastic materials, shifting then to produce boxes for fruit and vegetables and for the food sector.
Today our offer ranges from granules and technical compounds, to a complete range of technical articles for food and industrial packaging (cases, cassettes, cylindrical caps and flanges for coils of film, pallets) strictly in regenerated and recyclable plastic.
In general, our goal is to develop high-performance articles, also patented, using a lower quantity of material compared to analogous products on the market, so as to achieve savings and optimise production and recycling. But that’s not all: all our products are in polyolefin-based mono-material (PE and PP), as we are convinced that this is the only way to go in the direction of a real circular economy.
Rethinking production and products
For us, being sustainable means, most of all, innovating the production process.
The digitalisation of the company has enabled us to reduce production waste, as well as trace the entire production process as, moreover, requested by the European Community.
In practice, this implies that all our products have the date and production lot, the code of materials and whatever else is required by the regulations, as well as, if requested, a unique serial code and RFID tag.
Besides packaging for transport in an industrial, agri-food and pharmaceutical context,
we are working on an innovative packaging for the fish sector, which provides for direct contact with the food.
It is a box made up of the assembly of 2 parts: an internal tray in certified PP for food contact, an external box in recycled PP, with 25% calcium carbonate from shellfish shells, designed to last and to be reused over time.
What distinguishes Lucy Plast is having grown by developing customised projects which come into being as a result of real needs and, following this path, we have developed numerous original, but also economically sustainable, solutions.
The help of technology
The development of selection and regeneration technologies is, moreover, crucial for us, and allows us today to obtain a regenerated plastic which is 99% pure, when requested and, in any case, free of ferrous or dangerous materials.
This ensures greater speed in the injection-moulding process, as well as fewer problems with the moulds which, furthermore, we have made in Italy by specialised companies, with higher costs but also with better performance, and therefore less waste.
In addition, the dry granulation of plastic materials for moulding our packaging avoids further washing, thereby saving on water resources and reducing environmental impact.
It’s all a system that that has the effect of redeveloping and giving value to plastic material waste, which in this way becomes a precious resource, despite the fact that there is still a tendency to tar everything with the same brush, because it’s “useful” to give public opinion a bone to chew on…
Developing true sustainability
With regards, in fact, to environmental sustainability, contrary to what for years has been the “Plastic Free” trend, the data are clear: the management of plastic, if well done well, is less impactful in terms of energy consumption, CO2 emissions and water consumption compared to other materials.
There’s also a lot of misinformation and manipulation which has a negative effect on the entire packaging world.
We recuperate waste coming also from the food sector: packaging with direct contact with foods, such as snack wrappers.
Recently, some users have opted for wrappers made with coupled paper/plastic which are difficult to separate and which are creating significant problems.
A good choice, perhaps, from a marketing point of view, but short-sighted with regards to recycling, which benefits from the use of mono-materials.
The new frontiers
Summing up, for us a priority is to reduce the quantity of packaging material, use exclusively recycled mono-materials, optimise transport and storage, as well as have the tracing of products.
But now we are trying to go further. We want to use in the articles intended for a certain customer a certain percentage of their own waste, something which is useful for their own sustainability statement.
In addition, we are offering a service aimed at recovering customers’ industrial packaging from their final recipients throughout Europe, thereby completely eliminating disposal costs. The recovered packaging is then redelivered to the owners to be reused or, in the case of breakages, recycled by us.
After 18 months of experimentation, the data are encouraging: with only 8 projects currently ongoing, we have recovered more than 250,000 packages, recording, moreover, a breakage rate of 1.5%.
This seems to us to be a good example of the circular economy, but also a means to emphasise the value of packaging, demonstrating that plastic can be managed in a completely different way to how the general public is led to believe».